人民日报:依托技术创新和管理创新 绿色鞍钢正崛起
人民日报:依托技术创新和管理创新 绿色鞍钢正崛起
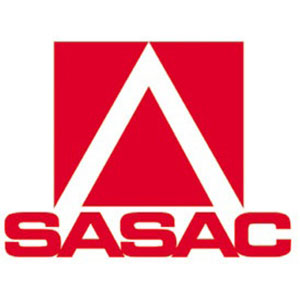
文章来源:人民日报 发布时间:2008-03-24
让“三废”资源化:一年吃掉100万辆轿车的废气
走进连绵的鞍钢厂区,最引人注目的是,一组30万千瓦的发电机组。
“这不是普通的发电机。”技术人员介绍,“它于2007年建成,是目前世界上功率最大、最先进的燃烧低热值高炉煤气联合循环发电机组(CCPP),年可发电23亿千瓦时,相当于一个年消耗70万吨标准煤热电厂的发电量,可将鞍钢剩余高炉煤气和焦炉煤气全部回收发电。而在以往,由于回收困难,只好向天空排放,仅这一项就成为鞍山的污染大户。”
2007年,鞍钢CCPP机组发电13亿多千瓦时;煤气回收总量近12亿立方米,减少二氧化碳排放100余万吨,相当于吃掉了100万辆小汽车一年排放的废气。
对钢铁行业来说,处理不停从高炉中排出来的低热值废气一直是难题:如任其散到空中,将造成严重大气污染;将废气处理净化,不但要投入大量资金,而且很难获得效益。引进这套机组,鞍钢投入了15亿元的巨资。“我们觉得值!中央企业应该更加主动地承担起节能减排的社会责任。”鞍钢负责人说。
如今,从利用冷却水(余热很高)供暖,到废气回收,鞍钢精心计算着生产过程中每一个能节能、减排的环节;完成了钢铁渣开发利用、OG泥及转炉煤气全回收、余热和水资源回收利用、粉尘冶金、建筑材料等“废水、废气、废渣”综合利用项目40多项,实现工业“三废”彻底资源化。
向科技要效益:“冠军炉”成为“下岗炉”
在鞍钢炼铁总厂,最醒目的莫过于一座容积达3200立方米的炼铁高炉。
这座高炉凝结着鞍钢人复杂的情结:有旧貌换新颜的喜悦,也有对“功臣”的怀念。
高炉的前身是一座几十年历史的“冠军炉”,容积1050立方米 ,无论产量、个头,还是效益,在冶金行业中都曾是排头兵,威名响当当。
2006年,国家淘汰落后产能,要求200立方米以下的高炉必须拆除。此时,鞍钢抓住国家调控机遇,提出“为了长远发展,必须将这座炼铁高炉关掉”的方案。顿时,公司上上下下情绪波动。
“心疼啊!当时效益那么好,扒掉能不心疼?但考虑到将来的生存,没有别的退路。”当时的炼铁总厂总工程师汤清华回忆说。
“冠军炉”倒了,3200立方米的新高炉拔地而起,粉尘零排放!污水零排放!耗水仅仅是老炉的1/54!
2006年底,鞍钢以壮士断腕的勇气,一次将3座容积在1100立方米以下的炼铁高炉全部停炉,淘汰落后产能210万吨,加上此前停用的4座高炉,鞍钢共计淘汰落后炼铁产能437万吨。经过技术改造,鞍钢现有高炉有效容积均达到2580立方米以上,打破了节能的最大瓶颈。
淘汰落后产能,为高附加值产品腾出了空间。十几年前,鞍钢高附加值产品不到10%,现在77%的产品是高附加值产品,能生产高强船板、高速重轨等700多个品种。
靠管理挖减排潜力:能源消耗实现实时监控
“这里就是推动鞍钢节能减排工作的‘神经中枢’。”站在鞍钢能源管控中心巨大的荧光屏前,鞍钢中心值班调度长马文勇一脸自豪。
鞍钢能源管控中心,实际上是一个大型信息平台,鞍钢集团去年投资1400万元新建。轻点鼠标,鞍钢钢铁生产全部环节的能源消耗、回收和二次利用情况,一目了然,全集团的能源利用情况都可以通过计算机控制,统一调配,综合平衡。
如今,鞍钢的节能减排理念已经从局部的修修补补,转向了整体推进的技术创新和管理创新。
“十五”以来,鞍钢实现节能380万吨标准煤,节水1.78亿吨;烟粉尘排放下降21%;二氧化硫排放下降12%;工业废水排放量减少49%。
鞍钢副总经理姚林说,钢铁作为高耗能和高污染行业,节能减排既是降低成本,提高核心竞争力的需要,又是企业必须履行的社会责任。预计到2009年,节能减排设备全部到位后,公司的能耗水平将跻身世界一流钢铁公司行列。