镇海炼化推进技术进步 实现炼油废水零排放目标
镇海炼化推进技术进步 实现炼油废水零排放目标
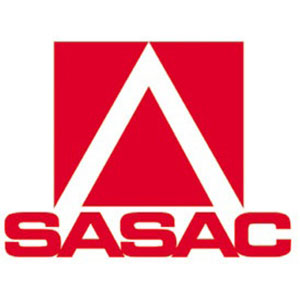
文章来源:中国石油化工集团公司 发布时间:2006-11-16
镇海炼化推进技术进步 基本实现炼油废水“零排放”目标
近年来,镇海炼化从强化管理、流程优化、热联合、低温热利用、运行优化入手,积极推进技术进步,有效地促进了能源的节约。
2005年镇海炼化共加工原油1710万吨,比2000年增加了62.86%,炼油实际能耗由71.13千克标油/吨下降到62.3千克标油/吨,相当于节油约15万吨/年;加工损失率由1.03%下降到0.63%,相当于节油6.84万吨/年;吨原油新鲜水耗量由1.5吨左右下降到0.42吨,相当于少消耗新鲜水1847万吨/年;吨油废水排放量由0.55吨下降到0.07吨,相当于少排放污水821万吨/年,基本实现炼油工业废水“零排放”的目标,达到了世界先进水平。
针对高硫原油和劣质原油逐年增加的情况,镇海炼化通过对炼油及化工工艺总流程的优化,构建了“常减压—加氢精制、加氢裂化(催化裂化)—硫磺回收”、“焦化—CFB锅炉”、“溶剂脱沥青—脱油沥青气化—脱沥青油加氢”等具有镇海炼化特色的高硫原油优化加工路线,最大限度做到物尽其用。镇海炼化与石科院、抚顺石化研究院联合开发了国内首创、列入总部“十条龙”攻关项目的“溶脱组合工艺”,构建了“溶剂脱沥青—脱油沥青气化—脱沥青油加氢”组合加工工艺,一举解决了渣油处理能力不足、蜡油资源不足、化肥原料劣质化三大技术难题,月均产生直接经济效益1113万元,每年累计创效上亿元。通过“焦化—CFB锅炉”加工路线,使劣质渣油不仅转化为液化气、汽油、柴油、蜡油等产品,提高了轻油收率,而且其副产品高硫石油焦也成为CFB锅炉的燃料,提高了综合商品率。在满足公司自身用电的基础上,还向社会供电,支援地方经济建设。通过构建“常减压—加氢精制、加氢裂化(催化裂化)—硫磺回收”工艺路线,既减少了二氧化硫排放量,又变废为宝,生产了14.9万吨商品硫磺。
镇海炼化通过对装置技术改造,不断提升装置运行水平,降低各类消耗。镇海炼化从设计开始就确保将装置建成能源节约型装置。PX装置歧化单元原设计能耗为54.1千克标油/吨,镇海炼化组织科技人员在吃透原工艺包的基础上,与研究单位一起对工艺包进行了大胆的优化创新,将甲苯塔、二甲苯塔顶、邻二甲苯塔顶和重芳烃塔顶由空冷冷却改为发生蒸汽,使装置塔顶热源基本得到回收。经标定,歧化单元标定能耗仅为43.72千克标油/吨,达到了国际先进水平。
镇海炼化抓好公用工程的优化运行,向系统节能降耗要效益。为减少制氢损失,他们在2002年实现单套制氢运行及原料100%气体化的基础上,围绕停运制氢装置实施了多项措施,当年,加工损失率即下降到0.63%,比2000年1.03%下降0.4个百分点,实际下降幅度达到38.8%,相当于节油6.38万吨。
镇海炼化成功开发了“节水减排成套技术”,为深化节水减排工作提供了有力的技术支撑。通过分质、分压、分系统回用,镇海炼化炼油凝结水回收率达到了65%,化工凝结水的回收率达到了89%;通过含硫污水的串级使用、汽提净化污水的回用、清净废水的利用等措施,2005年工业用水重复利用率达到了98.3%;开发污水回用技术,充分利用污水资源,将达标外排污水经适度处理后回用作循环水补充水,使炼油装置的4个循环水场100%使用回用污水,结束了以新鲜水为补充水的历史。2005年,回用污水549.2万吨,吨原油工业废水排放量0.07吨,吨原油新鲜水耗量0.42吨,达到了国际先进水平。